PPAP HOME

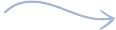
Design Documentation
PPAP involves the creation and submission of a comprehensive set of documents that demonstrate the supplier's understanding of the customer's requirements and their ability to meet those requirements.

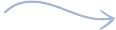
Design Failure Mode and Effects Analysis
Design Failure Mode and Effect Analysis (DFMEA) is an application of the Failure Mode and Effects Analysis (FMEA) that is specific to the design stage. The DFMEA allows the design team to document what they predict about a product's potential failures.

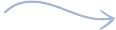
Process Flow Diagram
A process flow diagram or process pap is a graphical representation of a process. It serves as a tool to facilitate communication and understanding of the process. All steps in manufacturing process including components, measurement, and inspection.

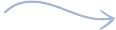
Process Failure Mode
and Effect Analysis
Prediction of a potential process failure that could occur during production. Prediction of a potential process failure that could occur during production.

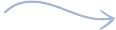
Control Plan
The Control Plan is an output from the PFMEA. The Control Plan lists all product Special Characteristics and inspection methods required to deliver products that continually meet the customer quality requirements.

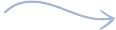
Measurement System Analysis
Measurement system analysis is a technique used to measure the variability of a process. The analysis will provide you with the mean and standard deviation to help you understand your process.

Checking aids
Checking aids are used by production and are a detailed list of all the tools used to inspect test or measure parts during the assembly process. This aid will list the part, describe the tool, and have the calibration schedule for the tool.
Customer Specific Requirements
This element of the submission package is where any special customer requirements are contained. For bulk materials, the customer specific requirements shall be recorded on the “Bulk Material Requirements Checklist”.
Dimension Layout Results
A list of every dimension on the ballooned part drawing and measurement results. This list includes the product characteristic, specification, measurement results, and assessment showing if the dimension “passed” or “failed”.
Records of Materials or
Performance Test
All tests that have been performed on the part shall be documented in this summary, including any pass or fail inspection results. This summary shall be signed off by the customer and the supplier to certify that all required tests have been completed.
Initial Process Studies
Initial process studies will be done on all the production processes and will include Statistical Process Control (SPC) charts on the critical characteristics of the product. These studies demonstrate that the critical processes are stable, demonstrate normal variation and are running near the intended nominal value.


Qualified Laboratory Documentation
Includes all of the industry certifications for any lab that was involved in completing validation testing.
Appearance Approval Report
The appearance approval report confirms that the customer has examined the final product and it satisfies all the necessary appearance specifications for the design. The report encompasses color, textures, fit (gaps between parts), etc.


Engineering Change Documentation
If the PPAP is being required due to a request for a change to a part or product, the documentation requesting and approving the change must be included in the PPAP package. This documentation usually consists of a copy of the Engineering Change Notice (ECN), which must be approved by the customer engineering department.
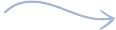
Customer Engineering Approval
This approval is usually the engineering trial with sample production parts performed by the customer. A "temporary deviation" is often required to send parts to the customer before the PPAP is complete.
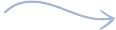
Level of Submission
Level 1: Only the client receives the Part Submission Warrant (PSW).
Level 2: Product samples and limited supporting documentation provided by PSW.
Level 3: PSW with all necessary supporting documentation and product samples.
Level 4: PSW and additional specifications as specified by the client.
Level 5: PSW at the supplier's manufacturing site, ready for inspection along with product samples and any necessary supporting documentation.
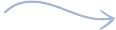
Part Submission Warrant
The PSW is a formal document included in the PPAP submission, confirming that the supplier's parts meet the customer's requirements and are ready for production. It provides a clear declaration of compliance.